Custom tig welding has become an essential process in modern manufacturing and fabrication industries, offering unparalleled precision and versatility. Whether you're a hobbyist or a professional welder, mastering this technique can significantly enhance your skills and project quality. This comprehensive guide will take you through everything you need to know about custom tig welding, from the basics to advanced tips.
Tig welding, also known as Tungsten Inert Gas welding, is a highly specialized welding process that allows for precision in joining metals. Its ability to create clean, high-quality welds makes it a favorite among professionals and enthusiasts alike. In this article, we will explore the nuances of custom tig welding, including its applications, techniques, and the tools required for success.
As we delve deeper into the world of custom tig welding, you'll discover how this process has revolutionized the way we approach metal fabrication. Whether you're working on automotive restoration, artistic sculptures, or industrial components, custom tig welding offers the flexibility and control necessary to achieve exceptional results.
Read also:Comprehensive Guide To Dmv Deerfield Everything You Need To Know
What is Custom Tig Welding?
Custom tig welding refers to the practice of using TIG welding techniques to create unique, tailored projects. This process involves the use of a non-consumable tungsten electrode to produce the weld, combined with an inert gas shield to protect the weld area from contamination. The precision and control offered by TIG welding make it ideal for custom applications.
Some key advantages of custom tig welding include:
- Precision control over weld parameters
- Ability to weld a wide range of materials, including stainless steel, aluminum, and titanium
- Clean and aesthetically pleasing welds
- High-quality, durable joints
According to industry experts, custom tig welding is increasingly being used in niche applications where traditional welding methods fall short. This trend highlights the growing demand for specialized welding skills in various industries.
Applications of Custom Tig Welding
The versatility of custom tig welding makes it suitable for a wide range of applications across different sectors. Below are some of the most common uses:
Automotive Restoration
Tig welding is widely used in automotive restoration projects due to its ability to produce clean, precise welds on thin materials. This is particularly important when working on vintage cars, where maintaining the original appearance is crucial.
Artistic Metalwork
Artists and metalworkers often rely on custom tig welding to create intricate designs and sculptures. The process allows for detailed work and seamless joins, making it ideal for artistic applications.
Read also:Pooping At Work Meme The Ultimate Guide To Humor In The Workplace
Industrial Fabrication
In industrial settings, custom tig welding is used to fabricate high-strength components that require precise tolerances. This includes applications in aerospace, marine, and energy sectors, where durability and reliability are paramount.
Tools and Equipment for Custom Tig Welding
To get started with custom tig welding, you'll need the right tools and equipment. Here's a list of essential items:
- Tig welding machine
- Tungsten electrode
- Inert gas supply (argon or helium)
- Welding torch
- Protective gear (gloves, helmet, and clothing)
Investing in high-quality equipment is crucial for achieving professional results. Modern tig welding machines often come with advanced features such as pulse control and digital interfaces, which enhance precision and ease of use.
Basic Techniques in Custom Tig Welding
Mastery of basic techniques is essential for successful custom tig welding. Below are some key techniques to focus on:
Proper Torch Angle
Maintaining the correct torch angle is critical for achieving a clean weld. A typical angle of 15-20 degrees is recommended for most applications.
Weld Pool Control
Controlling the size and shape of the weld pool is vital for producing strong, uniform joints. Practice adjusting the amperage and travel speed to achieve the desired results.
Filler Metal Addition
When adding filler metal, ensure it is introduced smoothly and consistently into the weld pool. This helps prevent defects such as porosity and undercutting.
Advanced Tips for Custom Tig Welding
Once you've mastered the basics, you can explore advanced techniques to further enhance your skills:
Pulse Welding
Pulse welding involves alternating between high and low currents during the welding process. This technique is useful for controlling heat input and reducing distortion, especially when working on thin materials.
Remote Amperage Control
Using a remote amperage control allows you to adjust the current while welding, providing greater flexibility and precision. This is particularly beneficial when working on complex or intricate projects.
Weld Inspection Techniques
Regular inspection of welds is essential to ensure quality and identify potential defects. Techniques such as visual inspection, dye penetrant testing, and ultrasonic testing can help detect issues early in the process.
Common Challenges in Custom Tig Welding
Like any skill, custom tig welding comes with its own set of challenges. Below are some common issues and how to address them:
Contamination of the Weld Area
Contamination can lead to weak or brittle welds. To avoid this, ensure the weld area is thoroughly cleaned before starting and use an adequate gas shield to protect the weld zone.
Porosity
Porosity occurs when gas becomes trapped in the weld pool, creating small holes. This issue can be minimized by maintaining a clean work area and using the correct gas flow rate.
Cracking
Cracks in welds can result from excessive heat input or improper cooling. To prevent cracking, control the heat input and allow the weld to cool gradually.
Safety Considerations in Custom Tig Welding
Safety should always be a priority when performing custom tig welding. Here are some important safety tips:
- Wear appropriate protective gear, including gloves, helmets, and fire-resistant clothing.
- Ensure adequate ventilation in the work area to prevent exposure to harmful fumes.
- Follow manufacturer guidelines for equipment operation and maintenance.
By adhering to these safety practices, you can minimize the risk of accidents and ensure a safe working environment.
Cost Considerations for Custom Tig Welding
Custom tig welding can be a significant investment, both in terms of equipment and time. Below are some factors to consider:
Initial Equipment Costs
The cost of tig welding equipment can vary widely depending on the brand and features. Entry-level machines typically start at $500, while professional-grade units can cost several thousand dollars.
Material Costs
The cost of materials, including tungsten electrodes, filler metals, and inert gases, should also be factored into your budget. Prices can fluctuate based on market conditions and availability.
Training and Certification
Investing in training and certification can improve your skills and increase your earning potential. Many welding schools and organizations offer courses specifically focused on tig welding techniques.
Future Trends in Custom Tig Welding
The field of custom tig welding is constantly evolving, with new technologies and techniques emerging regularly. Some key trends to watch include:
Automation and Robotics
Automation is increasingly being integrated into welding processes, offering improved efficiency and consistency. While this trend may impact traditional welding roles, it also creates opportunities for skilled welders to specialize in programming and maintenance.
Sustainable Practices
As environmental concerns grow, there is a push towards more sustainable welding practices. This includes the development of energy-efficient equipment and the use of eco-friendly materials.
Advanced Materials
The introduction of new materials, such as advanced alloys and composites, presents both challenges and opportunities for custom tig welders. Staying informed about these developments is crucial for maintaining competitiveness in the field.
Conclusion
Custom tig welding offers a unique blend of precision, versatility, and artistry that makes it an invaluable skill in today's manufacturing landscape. By understanding the basics, mastering advanced techniques, and staying informed about industry trends, you can excel in this field and achieve exceptional results.
We encourage you to share your thoughts and experiences in the comments below. Whether you're a seasoned professional or just starting out, your input can help others on their welding journey. Additionally, feel free to explore our other articles for more insights and tips on various welding techniques.
Table of Contents
- What is Custom Tig Welding?
- Applications of Custom Tig Welding
- Tools and Equipment for Custom Tig Welding
- Basic Techniques in Custom Tig Welding
- Advanced Tips for Custom Tig Welding
- Common Challenges in Custom Tig Welding
- Safety Considerations in Custom Tig Welding
- Cost Considerations for Custom Tig Welding
- Future Trends in Custom Tig Welding
- Conclusion
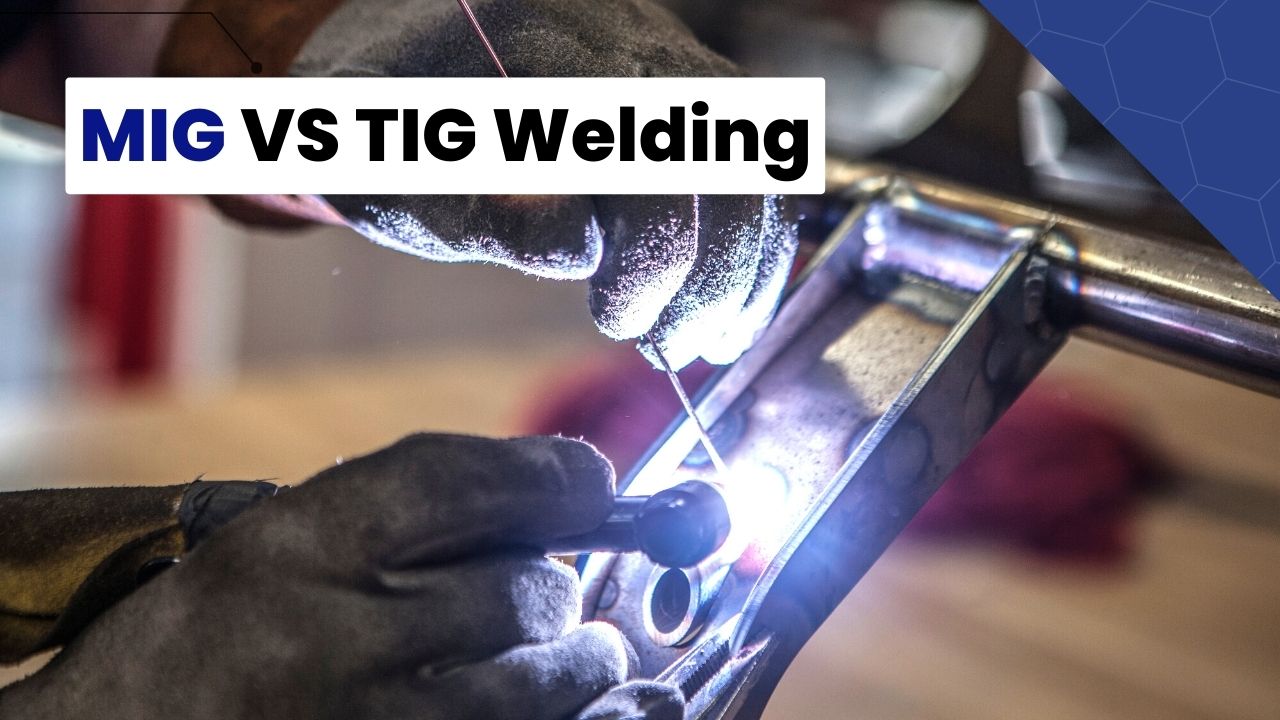
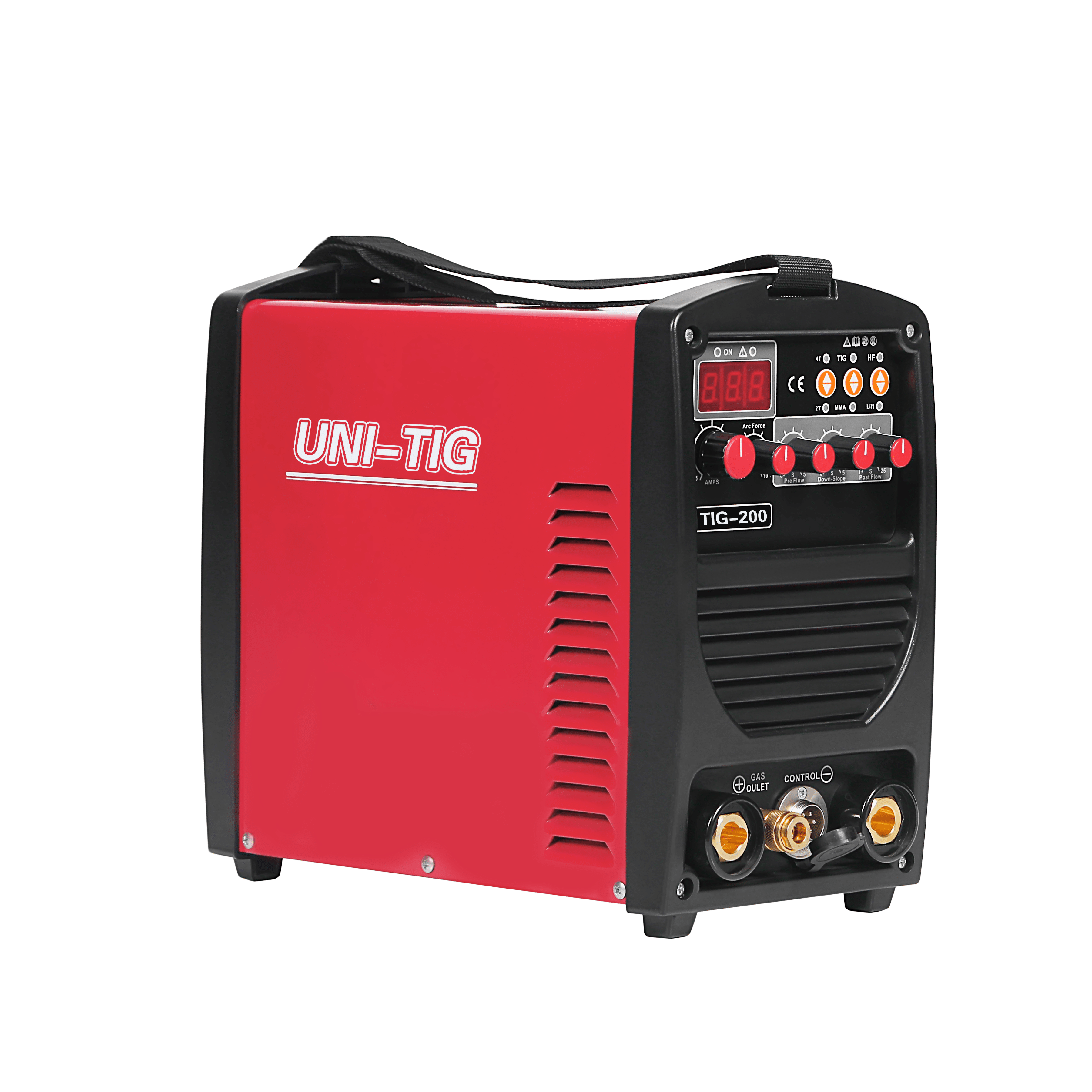
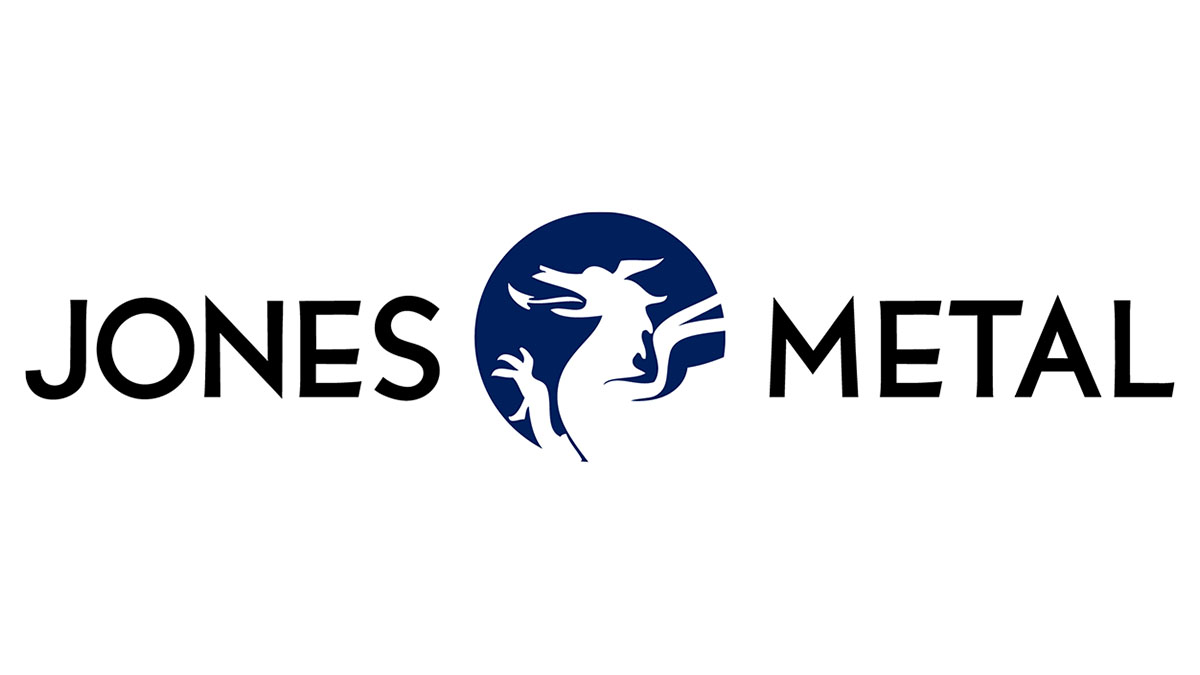